What are the Manufacturing Processes of the Latest Inductors?
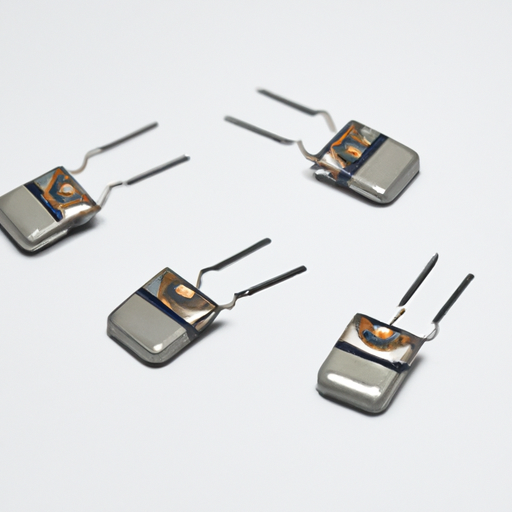
I. Introduction
Inductors are passive electronic components that store energy in a magnetic field when electrical current flows through them. They play a crucial role in various electronic circuits, including power supplies, radio frequency applications, and signal processing. As technology advances, the manufacturing processes of inductors have evolved significantly, leading to improved performance, efficiency, and miniaturization. This blog post will explore the latest manufacturing processes of inductors, highlighting the types, materials, innovations, challenges, and future trends in the industry.
II. Types of Inductors
Inductors come in various types, each designed for specific applications:
A. Air-core Inductors
These inductors do not use a magnetic core, relying solely on the air surrounding the coil to store energy. They are typically used in high-frequency applications due to their low losses.
B. Iron-core Inductors
Iron-core inductors utilize an iron core to enhance inductance. They are commonly used in power applications where higher inductance values are required.
C. Ferrite-core Inductors
Ferrite-core inductors use ferrite materials, which provide high magnetic permeability and low losses at high frequencies. They are widely used in RF applications.
D. Multilayer Inductors
These inductors consist of multiple layers of conductive and insulating materials, allowing for compact designs and high inductance values. They are often used in surface-mount technology (SMT).
E. Chip Inductors
Chip inductors are small, surface-mount devices that are ideal for compact electronic circuits. They are commonly used in mobile devices and other miniaturized applications.
F. Specialty Inductors
Specialty inductors, such as power inductors and RF inductors, are designed for specific applications, offering tailored performance characteristics.
III. Materials Used in Inductor Manufacturing
The performance of inductors is heavily influenced by the materials used in their construction:
A. Conductive Materials
1. **Copper**: The most common conductive material due to its excellent electrical conductivity.
2. **Aluminum**: Used in some applications for its lightweight properties and lower cost.
B. Magnetic Materials
1. **Ferrites**: Used in high-frequency applications for their high magnetic permeability and low losses.
2. **Iron Powder**: Provides good magnetic properties and is often used in power inductors.
3. **Laminated Steel**: Used in larger inductors to reduce eddy current losses.
C. Insulating Materials
1. **Polyimide**: A high-temperature resistant material used for insulation in various inductors.
2. **Epoxy Resins**: Commonly used for encapsulation and protection against environmental factors.
3. **Ceramic Substrates**: Used in multilayer inductors for their excellent insulating properties.
IV. Manufacturing Processes
The manufacturing of inductors involves several key processes:
A. Design and Prototyping
The first step in inductor manufacturing is design and prototyping. Engineers use computer-aided design (CAD) tools to create detailed models of the inductor. Simulation and modeling software help predict the performance of the inductor under various conditions, allowing for optimization before physical production begins.
B. Wire Winding
Wire winding is a critical step in inductor manufacturing. It can be done manually or through automated processes. The choice of technique often depends on the type of inductor being produced. For example, multilayer inductors may require specialized winding techniques to achieve the desired layer configuration.
C. Core Preparation
Core preparation involves selecting the appropriate core material and shaping it to fit the design specifications. This may include cutting, grinding, or treating the core material to enhance its magnetic properties.
D. Assembly
During the assembly phase, the wound wire is combined with the core. This process may involve soldering connections to ensure electrical continuity and mechanical stability.
E. Encapsulation and Coating
Encapsulation is essential for protecting inductors from environmental factors such as moisture and dust. Protective coatings are applied to enhance durability and reliability, with considerations for the specific application environment.
F. Testing and Quality Control
Quality control is vital in inductor manufacturing. Electrical testing ensures that the inductors meet performance specifications, while mechanical testing assesses their structural integrity. Reliability assessments are conducted to predict the lifespan and performance under various conditions.
V. Innovations in Inductor Manufacturing
The inductor manufacturing industry has seen several innovations in recent years:
A. Advances in Materials Science
New materials are being developed to enhance the performance of inductors. For example, advanced ferrite materials with improved magnetic properties are being used to create more efficient inductors.
B. Automation and Robotics in Production
Automation and robotics are increasingly being integrated into the manufacturing process, leading to higher precision, reduced labor costs, and increased production rates.
C. Miniaturization and Integration with Other Components
As electronic devices become smaller, the demand for miniaturized inductors has grown. Manufacturers are developing inductors that can be integrated with other components, such as capacitors and resistors, to save space on circuit boards.
D. Sustainable Manufacturing Practices
With a growing emphasis on sustainability, manufacturers are exploring eco-friendly materials and processes. This includes reducing waste, recycling materials, and using energy-efficient production methods.
VI. Challenges in Inductor Manufacturing
Despite advancements, the inductor manufacturing industry faces several challenges:
A. Supply Chain Issues
Global supply chain disruptions can impact the availability of raw materials, leading to delays in production and increased costs.
B. Cost Management
Balancing performance with cost is a constant challenge. Manufacturers must find ways to produce high-quality inductors without significantly increasing prices.
C. Meeting Industry Standards and Regulations
Compliance with industry standards and regulations is essential for ensuring product safety and reliability. Manufacturers must stay updated on changing regulations to avoid penalties.
D. Balancing Performance with Size and Cost
As the demand for smaller inductors increases, manufacturers must find ways to maintain performance while reducing size and cost. This often requires innovative design and material solutions.
VII. Future Trends in Inductor Manufacturing
Looking ahead, several trends are likely to shape the future of inductor manufacturing:
A. Emerging Technologies (e.g., 3D Printing)
3D printing technology is beginning to be explored for inductor manufacturing, allowing for rapid prototyping and the creation of complex geometries that were previously difficult to achieve.
B. The Impact of Electric Vehicles and Renewable Energy
The rise of electric vehicles and renewable energy sources is driving demand for high-performance inductors. Manufacturers will need to develop inductors that can handle higher power levels and operate efficiently in these applications.
C. The Role of IoT and Smart Devices in Inductor Design
The Internet of Things (IoT) and the proliferation of smart devices are creating new opportunities for inductor design. Manufacturers will need to focus on developing compact, efficient inductors that can support the growing number of connected devices.
VIII. Conclusion
In conclusion, the manufacturing processes of inductors have evolved significantly, driven by advancements in materials science, automation, and the demand for miniaturization. As technology continues to advance, the importance of inductors in electronic circuits remains paramount. Ongoing innovation in manufacturing processes will be essential to meet the challenges and opportunities presented by emerging technologies and market demands. The future of inductors in electronics looks promising, with continued advancements paving the way for more efficient, compact, and sustainable solutions.
IX. References
1. Academic journals on electrical engineering and materials science.
2. Industry reports from leading electronics manufacturers.
3. Manufacturer specifications and white papers on inductor technology and applications.