Common Production Processes for Tantalum Capacitors
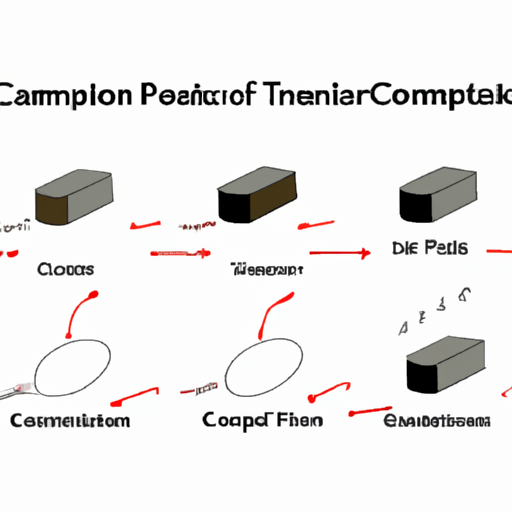
I. Introduction
A. Overview of Tantalum Capacitors
Tantalum capacitors are a type of electrolytic capacitor that utilizes tantalum metal for its anode. These capacitors are renowned for their high capacitance values, compact size, and excellent stability over a wide range of temperatures and frequencies. They play a crucial role in various electronic applications, including smartphones, computers, and automotive electronics, where reliability and performance are paramount.
B. Importance of Understanding Production Processes
Understanding the production processes of tantalum capacitors is essential for several reasons. First, the quality and reliability of electronic components directly influence the performance of the devices they are used in. Second, the production methods can significantly impact the electrical characteristics of the capacitors, such as capacitance, equivalent series resistance (ESR), and lifespan. By delving into the intricacies of tantalum capacitor production, we can appreciate the complexities involved in creating these vital components.
II. Raw Materials and Preparation
A. Tantalum Source Materials
The primary source of tantalum is tantalite ore, which contains tantalum oxide (Ta2O5). The extraction of tantalum from tantalite involves several methods, including hydrometallurgical and pyrometallurgical techniques. The ore is first crushed and then subjected to chemical processes to separate tantalum from other minerals.
Purification processes are critical to ensure that the tantalum is of high purity, typically above 99.9%. This is achieved through methods such as solvent extraction and ion exchange, which remove impurities that could adversely affect the performance of the final capacitor.
B. Other Materials Used
In addition to tantalum, other materials are essential in the production of tantalum capacitors. Dielectric materials, which form the insulating layer between the anode and cathode, are crucial for the capacitor's functionality. Common dielectric materials include tantalum oxide, which is formed during the anodization process.
Conductive materials, such as manganese dioxide or conductive polymers, are also used for the cathode. The choice of cathode material can significantly influence the capacitor's performance, including its ESR and overall efficiency.
III. Production Processes
A. Powder Production
The first step in the production of tantalum capacitors is the production of tantalum powder. This is typically achieved through the reduction of tantalum pentoxide (Ta2O5) using various methods.
1. Reduction of Tantalum Pentoxide (Ta2O5)
The reduction process involves converting tantalum pentoxide into metallic tantalum. This can be done using hydrogen or other reducing agents at high temperatures. The choice of reducing agent and the conditions under which the reduction occurs can affect the properties of the resulting tantalum powder.
2. Methods of Powder Production
There are two primary methods for producing tantalum powder:
Hydrometallurgical Methods: These methods involve the use of aqueous solutions to extract tantalum from its ores. The tantalum is then precipitated and dried to form a powder. This method is often favored for its ability to produce high-purity tantalum.
Pyrometallurgical Methods: In contrast, pyrometallurgical methods involve high-temperature processes to extract tantalum. This can include techniques such as carbothermic reduction, where tantalum oxide is reduced using carbon at elevated temperatures.
B. Pellet Formation
Once the tantalum powder is produced, the next step is pellet formation. This involves compressing the powder into a solid form, which will serve as the anode of the capacitor.
1. Pressing Techniques
Pellet formation typically involves pressing the tantalum powder into a desired shape using a die. The pressing process must be carefully controlled to ensure uniform density and shape, which are critical for the performance of the capacitor.
2. Sintering Processes
After pressing, the pellets undergo sintering, a process that involves heating them to a temperature below their melting point to promote bonding between the particles.
Temperature and Atmosphere Control: The sintering process must be conducted in a controlled atmosphere, often in a vacuum or inert gas environment, to prevent oxidation and contamination.
Effects on Density and Electrical Properties: The sintering conditions, including temperature and time, significantly affect the density and electrical properties of the tantalum anodes. Higher density typically leads to better performance characteristics.
IV. Anode Fabrication
A. Anode Preparation
The preparation of the tantalum anode is a critical step in the production of tantalum capacitors.
1. Formation of Tantalum Anodes
The sintered pellets are then machined to the desired dimensions and shapes, which can vary depending on the specific application of the capacitor.
2. Surface Treatment and Oxidation
Surface treatment is essential to enhance the performance of the anode. This often involves cleaning and etching the surface to improve the adhesion of the dielectric layer that will be formed during the anodization process.
B. Electrolytic Oxidation
Electrolytic oxidation is the process that forms the dielectric layer on the tantalum anode.
1. Formation of the Dielectric Layer
During this process, the tantalum anode is immersed in an electrolytic solution, and a voltage is applied. This causes tantalum oxide to form on the surface of the anode, creating a thin insulating layer.
2. Importance of Oxide Thickness and Quality
The thickness and quality of the oxide layer are critical for the capacitor's performance. A thicker oxide layer generally results in higher capacitance, but it must be carefully controlled to avoid breakdown.
V. Cathode and Encapsulation
A. Cathode Material Selection
The choice of cathode material is crucial for the overall performance of the tantalum capacitor.
1. Types of Cathode Materials
Common cathode materials include manganese dioxide and conductive polymers. Each material has its advantages and disadvantages, impacting the capacitor's ESR, stability, and temperature characteristics.
2. Impact on Capacitor Performance
The cathode material can significantly influence the capacitor's performance, including its efficiency, lifespan, and reliability under various operating conditions.
B. Encapsulation Techniques
Once the anode and cathode are prepared, the next step is encapsulation.
1. Coating Methods
Encapsulation involves applying protective coatings to the capacitor to prevent environmental damage and ensure reliability. Various coating methods, such as epoxy or ceramic coatings, can be used.
2. Packaging and Sealing Processes
The final packaging and sealing processes are critical to protect the capacitor from moisture and contaminants, which can lead to failure. This often involves hermetic sealing techniques to ensure long-term reliability.
VI. Quality Control and Testing
A. Quality Assurance Measures
Quality control is paramount in the production of tantalum capacitors to ensure they meet industry standards and customer expectations.
1. Standards and Certifications
Manufacturers often adhere to international standards, such as ISO 9001, to ensure consistent quality in their production processes.
2. In-Process Inspections
Regular in-process inspections are conducted to monitor the quality of materials and components at various stages of production.
B. Final Testing Procedures
Once the capacitors are assembled, they undergo rigorous testing to ensure they meet performance specifications.
1. Electrical Testing
Electrical testing involves measuring parameters such as capacitance, ESR, and leakage current to ensure the capacitors function as intended.
2. Reliability Testing
Reliability testing assesses the capacitors' performance under extreme conditions, including temperature cycling and humidity exposure, to ensure they can withstand real-world applications.
VII. Environmental and Safety Considerations
A. Environmental Impact of Tantalum Production
The production of tantalum capacitors raises several environmental concerns, particularly related to mining and extraction.
1. Mining and Extraction Concerns
Tantalum mining can have significant environmental impacts, including habitat destruction and pollution. Sustainable mining practices are essential to mitigate these effects.
2. Waste Management Practices
Effective waste management practices are crucial in the production process to minimize environmental impact and ensure compliance with regulations.
B. Safety Protocols in Manufacturing
Safety is a top priority in the manufacturing of tantalum capacitors.
1. Handling of Materials
Proper handling protocols must be established to ensure the safe use of tantalum and other materials involved in the production process.
2. Workplace Safety Measures
Workplace safety measures, including personal protective equipment (PPE) and training programs, are essential to protect workers from potential hazards.
VIII. Conclusion
A. Summary of Key Production Processes
The production of tantalum capacitors involves a series of intricate processes, from raw material extraction to final testing. Each step is critical to ensuring the quality and reliability of the final product.
B. Future Trends in Tantalum Capacitor Manufacturing
As technology continues to evolve, so too will the production processes for tantalum capacitors. Innovations in materials and manufacturing techniques are expected to enhance performance and sustainability. Additionally, the growing demand for compact and efficient electronic components will drive advancements in tantalum capacitor technology, ensuring their continued relevance in the electronics industry.
IX. References
- Academic Journals
- Industry Reports
- Manufacturer Guidelines
This comprehensive overview of the production processes for tantalum capacitors highlights the complexity and importance of each step in ensuring the quality and reliability of these essential electronic components. Understanding these processes not only enhances our appreciation of tantalum capacitors but also underscores the need for continued innovation and sustainability in their production.