Manufacturing Processes of the Latest Energy Storage Capacitors
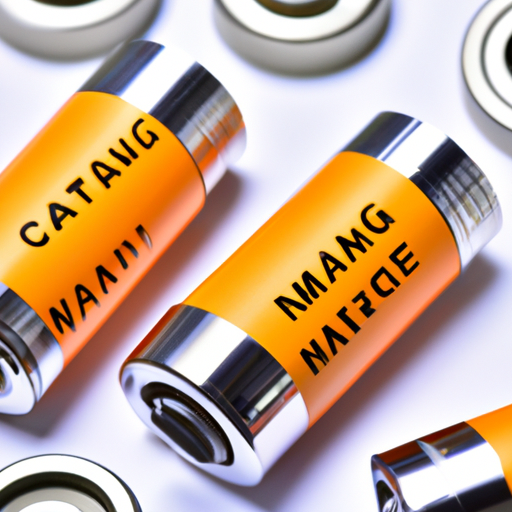
I. Introduction
Energy storage capacitors are essential components in modern electronic devices, enabling efficient energy management and delivery. These capacitors store electrical energy for later use, playing a crucial role in applications ranging from consumer electronics to renewable energy systems. As technology advances, the demand for more efficient, reliable, and compact energy storage solutions has led to significant innovations in capacitor technology. This blog post explores the manufacturing processes of the latest energy storage capacitors, highlighting the types, materials, techniques, and future trends in this dynamic field.
II. Types of Energy Storage Capacitors
A. Electrolytic Capacitors
Electrolytic capacitors are widely used for their high capacitance values and ability to store significant amounts of energy. They consist of two conductive plates separated by an electrolyte, which allows for a larger surface area and higher capacitance. Common applications include power supply circuits and audio equipment.
B. Ceramic Capacitors
Ceramic capacitors are known for their stability and reliability. They use a ceramic material as the dielectric, making them suitable for high-frequency applications. These capacitors are often found in RF circuits, decoupling applications, and timing circuits.
C. Film Capacitors
Film capacitors utilize a thin plastic film as the dielectric material. They are valued for their low self-inductance and high insulation resistance, making them ideal for applications requiring high voltage and stability, such as power electronics and motor drives.
D. Supercapacitors
Supercapacitors, or ultracapacitors, bridge the gap between traditional capacitors and batteries. They offer high energy density and rapid charge/discharge capabilities, making them suitable for applications like regenerative braking systems and energy harvesting.
E. Hybrid Capacitors
Hybrid capacitors combine features of both batteries and supercapacitors, offering a balance of energy density and power density. They are emerging as promising solutions for applications requiring both quick bursts of energy and longer-term storage.
III. Key Materials Used in Capacitor Manufacturing
A. Dielectric Materials
The dielectric material is crucial for capacitor performance. Common types include ceramic, plastic films, and electrolytic solutions. Each material has unique properties that affect capacitance, voltage rating, and temperature stability.
B. Conductive Materials
Conductive materials, such as aluminum, tantalum, and conductive polymers, are used for electrodes. The choice of material impacts the capacitor's efficiency, longevity, and overall performance.
C. Electrolytes
Electrolytes can be liquid or solid, depending on the capacitor type. Liquid electrolytes are often used in electrolytic capacitors, while solid electrolytes are common in supercapacitors and hybrid capacitors, offering improved safety and stability.
D. Substrates and Packaging Materials
The substrate provides structural support for the capacitor, while packaging materials protect the internal components. Innovations in these materials can enhance durability and thermal management.
IV. Manufacturing Processes
A. Material Preparation
The manufacturing process begins with sourcing and processing raw materials. Quality control measures are essential to ensure that materials meet the required specifications for performance and safety.
B. Dielectric Layer Formation
The dielectric layer is critical for capacitor function. Various techniques are employed for its deposition:
1. **Chemical Vapor Deposition (CVD)**: This method involves depositing a thin film of dielectric material onto a substrate through chemical reactions in a vapor phase.
2. **Physical Vapor Deposition (PVD)**: PVD techniques, such as sputtering, involve the physical transfer of material from a source to the substrate, creating a thin film.
3. **Sol-Gel Processes**: This technique allows for the creation of dielectric materials through a solution that transforms into a solid gel, offering flexibility in material composition.
C. Electrode Fabrication
Creating electrodes is a critical step in capacitor manufacturing. Various methods are used:
1. **Screen Printing**: This technique allows for precise application of conductive materials onto substrates, ideal for mass production.
2. **Stamping and Etching**: These methods involve cutting and shaping conductive materials to form electrodes, ensuring high precision.
3. **Sputtering**: A PVD technique that deposits thin layers of conductive material onto the dielectric layer, enhancing electrode performance.
D. Assembly of Capacitors
The assembly process involves stacking and aligning the dielectric and electrode layers. Encapsulation and sealing techniques are employed to protect the internal components from environmental factors, ensuring longevity and reliability.
E. Testing and Quality Assurance
Quality assurance is vital in capacitor manufacturing. Electrical testing methods assess capacitance, leakage current, and equivalent series resistance (ESR). Reliability testing ensures that capacitors can withstand operational stresses, while compliance with industry standards guarantees safety and performance.
V. Innovations in Manufacturing Techniques
A. Automation and Robotics
The integration of automation and robotics in capacitor manufacturing has significantly improved efficiency and precision. Automated systems can handle repetitive tasks, reducing human error and increasing production rates.
B. Advanced Materials
The use of nanomaterials in capacitor manufacturing is a growing trend. These materials can enhance performance characteristics, such as energy density and charge/discharge rates, leading to more efficient energy storage solutions.
C. Sustainable Manufacturing Practices
Sustainability is becoming increasingly important in capacitor manufacturing. Companies are adopting practices to reduce waste and energy consumption, as well as exploring recycling and reusability of materials to minimize environmental impact.
VI. Challenges in Capacitor Manufacturing
A. Cost of Advanced Materials
While advanced materials can enhance performance, they often come with higher costs. Balancing performance and affordability is a significant challenge for manufacturers.
B. Scalability of New Technologies
Innovative manufacturing techniques may face scalability issues. Developing processes that can be efficiently scaled for mass production is crucial for widespread adoption.
C. Environmental Concerns
Manufacturers must address environmental concerns related to material sourcing, production waste, and end-of-life disposal. Implementing eco-friendly practices is essential for sustainability.
D. Competition with Alternative Energy Storage Solutions
As energy storage technologies evolve, capacitors face competition from batteries and other energy storage solutions. Manufacturers must continuously innovate to maintain their relevance in the market.
VII. Future Trends in Energy Storage Capacitors
A. Research and Development Directions
Ongoing research is focused on improving energy density, charge/discharge rates, and overall performance of capacitors. Innovations in materials and manufacturing processes will drive future advancements.
B. Potential Market Growth and Applications
The market for energy storage capacitors is expected to grow, driven by increasing demand in electric vehicles, renewable energy systems, and consumer electronics. New applications will continue to emerge as technology evolves.
C. Integration with Renewable Energy Sources
Capacitors will play a vital role in integrating renewable energy sources into the grid. Their ability to provide rapid energy storage and release will support the stability and reliability of renewable energy systems.
VIII. Conclusion
The manufacturing processes of energy storage capacitors are evolving rapidly, driven by advancements in materials, techniques, and technology. As the demand for efficient energy storage solutions continues to grow, ongoing innovation in capacitor technology will be essential. By addressing challenges and embracing new trends, manufacturers can ensure that energy storage capacitors remain a vital component in the future of energy management.
IX. References
1. Academic journals on capacitor technology and materials science.
2. Industry reports on energy storage solutions and market trends.
3. Relevant books and articles discussing advancements in capacitor manufacturing processes.
This comprehensive overview of the manufacturing processes of the latest energy storage capacitors highlights the importance of innovation and adaptation in a rapidly changing technological landscape. As we look to the future, the role of capacitors in energy storage will only become more significant, paving the way for a more sustainable and efficient energy ecosystem.